Loading Docks, Ceiling Heights, and Power Requirements: Understanding Industrial Property Specs
Loading Docks and Access Points
Types of Loading Configurations
When searching for industrial space, understanding property specifications is essential for finding a facility that meets your operational needs. Three critical factors- loading docks, ceiling heights, and power requirements can make or break a property’s suitability for your business. This guide explains these key specifications in detail to help you evaluate potential properties effectively.
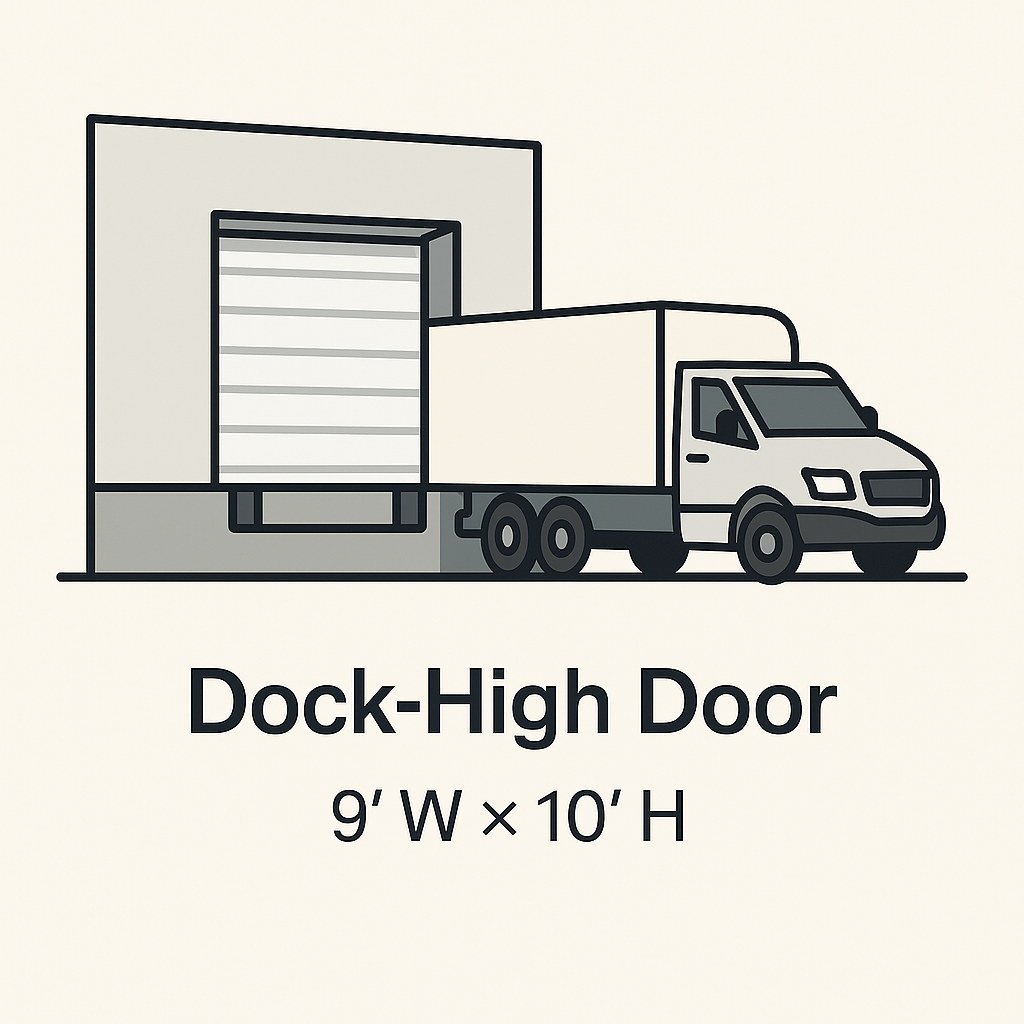
Dock-High Doors
- Description: Elevated doors positioned 48-52 inches above ground level
- Ideal for: Businesses receiving deliveries from semi-trailers
- Key measurements: Standard door dimensions are 8’W × 10’H or 9’W × 10’H
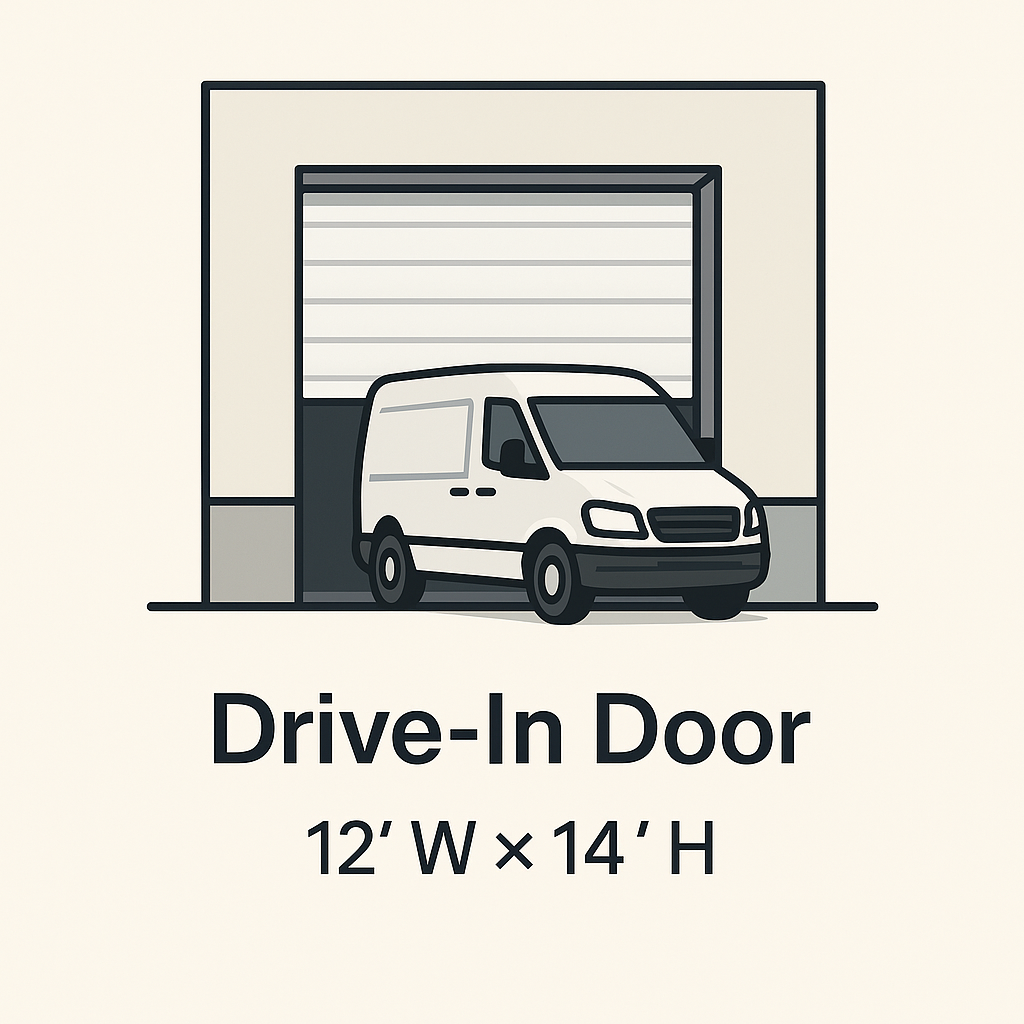
Drive-In or Grade-Level Doors
- Description: Ground-level doors allowing direct vehicle access
- Ideal for: Businesses using vans, pickup trucks, or forklifts for loading/unloading
- Key measurements: Typically 12’W × 14’H or 14’W × 16’H
Loading Dock Equipment
Dock Levers | Dock Seals | Dock Bumpers |
Bridge the gap between the truck and the building | Create a weather-tight barrier around trucks | Protects the building and vehicle during docking |
Different types include; hydraulic, mechanical, and air-powered | Different types include: compression seals (foam pads that compress) and shelters (canopy-style coverings) | Different types include: Molded rubber, laminated rubber, steel-faced |
Capacity typically falls between 25,000 to 50,000 pounds | Benefits: reduce energy costs and protect products from any weather | Typically 7’4″ apart for standard trailer positioning |
Truck Court Considerations

Apron Depth
- Definition: Distance from the building to the opposite edge of the truck court
- Minimum requirements:
- 120′ for standard trailers with adequate maneuvering space
- 130’+ for extended trailers or busy operations
- 170’+ for situations requiring trailer storage
Turning Radius
- Requirements:
- Standard 53′ trailer: Approximately 105′ outside turning diameter
- City delivery trucks: 45-65′ turning diameter
- Consideration of entry points from public streets
Loading Position Ratios
Industry Standards
- Distribution centers: 1 dock position per 5,000-10,000 sq ft
- Manufacturing: 1 dock position per 15,000-20,000 sq ft
- Light industrial/flex: 1 dock position per 8,000-12,000 sq ft
Strategic Factors
Higher ratios needed for:
- Cross-docking operations
- High inventory turnover
- Just-in-time manufacturing
- Multiple daily deliveries
Ceiling Heights
Understanding Clear Height Measurements
Definition and Measurement
- Clear height: Usable height from floor to lowest overhead obstruction
- Obstruction examples: Joists, trusses, sprinklers, lights, HVAC
- Building height: Typically 2-4 feet greater than clear height
How Clear Height Affects Operations
- Storage capacity: Each additional foot of clear height adds 7-10% storage capacity
- Racking options: Determined by forklift reach and clear height
- Cubic footage calculation: Length × Width × Clear Height = Usable Volume
Industry Standards by Use
Distribution and Fulfillment
- Modern standards: 32-40+ feet clear
- E-commerce requirements: Often 36-40+ feet
- Older buildings: 24-28 feet
- Legacy warehouses: 18-24 feet
Manufacturing
- Light manufacturing: 18-24 feet typically sufficient
- Heavy manufacturing: 24-30+ feet for equipment clearance
- Specialized needs: Equipment-specific requirements
Mixed-Use and Flex Space
- Standard range: 16-24 feet
- Office components: Often 9-12 feet drop ceilings
- Special considerations: Mezzanine potential in higher spaces
Clear Height Premium
Market Value Impact
- Rent premium: Each additional foot of clear height typically adds $0.15-$0.30/sq ft to annual rent
- Modern vs. legacy: Premium buildings (36’+ clear) command 20-30% higher rates than older buildings (24′ clear)
Operating Cost Effects
- Heating/cooling: Higher spaces cost more to condition
- Lighting: More fixtures/power required for taller spaces
- Sprinkler systems: Higher clear heights require more extensive coverage
Specialized Ceiling Features
Crane Systems
- Requirements:
- Hook height specifications
- Capacity requirements (tonnage)
- Span distance needed
- Building impact: Requires reinforced structure, often reduces clear height
Mezzanines
- Purpose: Adds usable square footage within existing footprint
- Structural implications: Building must support additional load
- Clearance needs: Typically requires minimum 24′ clear height to be practical
Power Requirements
Electrical System Basics
Service Types
- Single-phase power: 120/240V, suitable for basic lighting, HVAC, office equipment
- Three-phase power: 208V, 240V, or 480V, required for most industrial equipment
- High-voltage service: 600V+, specialized manufacturing applications
Capacity Measurements
- Amperage: Total current capacity (e.g., 400 amp, 800 amp, 1200 amp service)
- Voltage: Electrical pressure/potential
- Phase: Method of power distribution (single or three-phase)
Typical Requirements by Use
Use Type | Service | Density | Sufficient For |
Light Industrial/Flex | 200-400 amp, 120/208V, three-phase | 5-10 watts per square foot | Small equipment, standard lighting, basic HVAC |
General Warehousing | 400-600 amp, 277/480V, three-phase | 10-15 watts per square foot | Conveyor systems, charging stations, lighting, HVAC |
Manufacturing | 800-2000+ amp, 277/480V, three-phase | 20-50+ watts per square foot | Heavy equipment |
Data Center/High-Tech | 2000+ amp, redundant feeds | 100-200+ watts per square foot | Servers, cooling systems |
Assessing Existing Power Infrastructure
Service Verification
- Main disconnect rating: Shows total amperage capacity
- Transformer size: Indicates maximum available power
- Panel schedule: Lists circuits and capacities
- Utility records: Confirm actual service specifications
Power Distribution
- Bus duct: Overhead power distribution system
- Panel locations: Proximity to equipment placement
- Sub-panels: Capacity and locations throughout facility
Upgrade Considerations
- Utility capacity: Available power at street/property
- Transformer requirements: Size, cost, location, ownership (utility or tenant)
- Upgrade timeline: Often 3-9 months for significant increases
- Cost factors: Can range from $50,000 to $500,000+ for major upgrades
Special Power Considerations
Backup Power
- Generator compatibility: Space and connections for emergency power
- Transfer switch location: Required for generator integration
- Critical load assessment: Determining essential systems
Sustainable Energy Options
- Solar readiness: Roof structural capacity, orientation
- EV charging infrastructure: Capacity for vehicle charging stations
- Energy storage compatibility: Space and connections for battery systems
How These Specs Work Together
Operational Assessment
Before evaluating properties, determine your specific requirements:
- Loading needs: Daily truck traffic, types of vehicles, loading patterns
- Storage strategy: Racking systems, stacking heights, cubic capacity needs
- Equipment list: Voltage, phase, and amperage for all machinery
Property Evaluation Checklist
When touring potential properties, verify:
- Loading dock measurements: Door dimensions, dock height, leveler condition
- Truck court sufficiency: Measure apron depth, observe traffic patterns
- Clear height confirmation: Measure at multiple points, note obstructions
- Power verification: Check transformer, main disconnect, available distribution
Future-Proofing Considerations
Consider how your needs might evolve:
- Growth projections: Will your shipping volume increase?
- Equipment upgrades: Will future machinery require more power?
- Storage efficiency: How might inventory levels change?
Common Pitfalls and Solutions
Loading Area Issues | Ceiling Height Limitations | Power Supply Challenges |
Problem: Insufficient Truck Court Depth | Problem: Insufficient Stacking Height | Problem: Undersized Electrical Service |
Signs: Difficult trailer positioning, traffic congestion Solutions: Staggered shipping/receiving schedule Traffic management system Consider smaller delivery vehicles where possible | Signs: Excessive floor space used for storage, inefficient layout Solutions: Narrow aisle racking systems Mezzanine installation where height permits More frequent inventory turnover | Signs: Circuit trips, inability to run all equipment simultaneously Solutions: Load management systems Staggered equipment operation Service upgrade (if feasible) |
Problem: Inadequate Number of Docks | Problem: Obstructions Below Listed Clear Height | Problem: Incorrect Voltage or Phase |
Signs: Loading backups, extended wait times Solutions: Installing additional dock positions (if building allows) Implementing appointment scheduling Off-peak shipping/receiving hours | Signs: Unable to fully utilize vertical space Solutions: Custom racking design around obstructions Relocation of HVAC or utilities where possible Strategic layout planning | Signs: Equipment cannot operate properly Solutions: Phase converters (limited applications) Transformers for voltage adjustment Utility service upgrade |
Examples
Distribution Company Expansion
A growing distribution company needed to move from a 15,000 sq ft facility with 24′ clear height to accommodate increasing inventory.
Key requirements:
- 30’+ clear height for taller racking
- Multiple dock doors for concurrent loading/unloading
- Adequate power for conveyor systems and charging stations
Solution found:
- 40,000 sq ft facility with 32′ clear height
- 8 dock doors with hydraulic levelers
- 800 amp, 277/480V service
- Result: 175% increase in storage capacity despite only 167% increase in square footage
Manufacturing Facility Relocation
A precision manufacturing company needed to relocate from an outdated facility that couldn’t support their specialized equipment.
Key requirements:
- 1200 amp, 480V three-phase power
- 24’+ clear height for equipment
- Drive-in doors for machinery movement
- Heavy floor load capacity
Solution found:
- Former distribution center converted to manufacturing
- Power upgraded from 600 amp to 1500 amp service
- Two new 14’×16′ drive-in doors added
- Floor reinforced in key production areas
- Result: 30% increase in production capacity in the new facility
Conclusion
Loading docks, ceiling heights, and power requirements might seem like technical details, but they fundamentally determine whether an industrial property can support your business operations effectively. Understanding these specifications enables you to:
- Quickly eliminate unsuitable properties from consideration
- Accurately estimate improvement costs for properties that need modifications
- Negotiate leases with clear knowledge of a property’s actual value to your operations
- Plan for efficient operations from day one in your new facility
When evaluating industrial properties, remember that renovating basic building characteristics like clear height is often prohibitively expensive, while adding dock positions or upgrading power can be feasible with the right budget and timeline. Focus on finding a property where the fundamental specifications meet your needs, then consider modifications for less critical elements.