The Ultimate Guide to Cross-Docking Facilities: When to Use Them and How to Find Them
Cross-docking has transformed logistics operations for businesses of all sizes, enabling faster delivery times, reduced storage costs, and streamlined supply chains. This guide explains everything you need to know about cross-docking facilities, from basic concepts to finding the perfect location for your operation.
What Is Cross-Docking?
Cross-docking is a logistics practice where products from a supplier or manufacturer are distributed directly to a customer or retail chain with minimal to no storage time. Products arrive at a dock on one side of the facility and leave from another dock, typically within 24 hours.
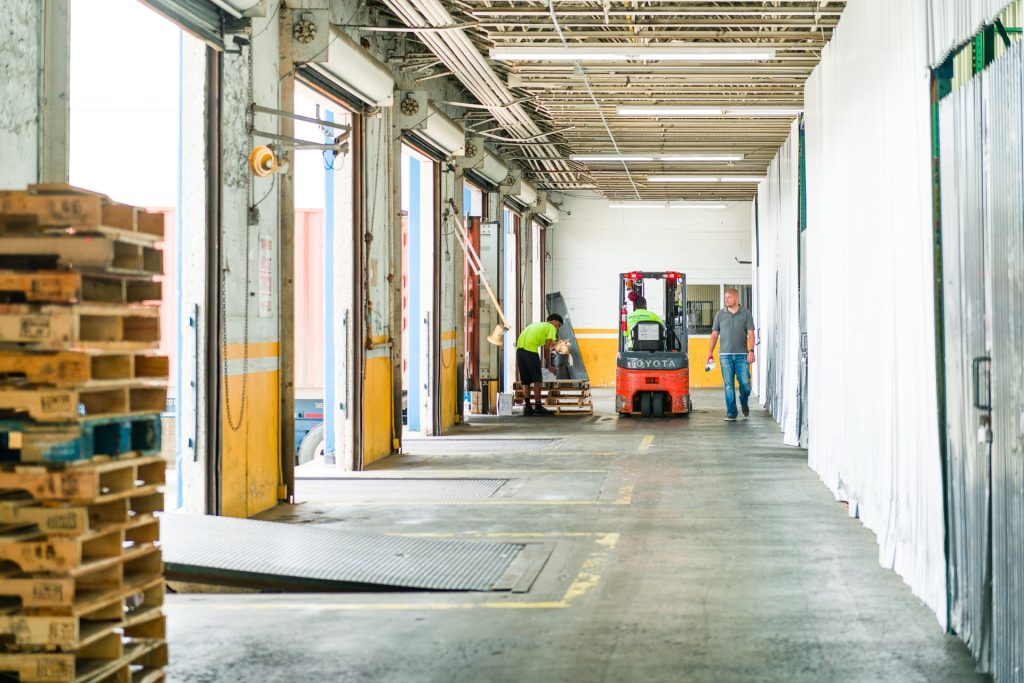
The Core Process:
- Inbound shipments arrive at receiving docks
- Products are sorted, scanned, and reorganized based on the destination
- Items are moved directly across the dock to the appropriate outbound loading area
- Outbound shipments depart to their final destinations
This process eliminates traditional warehousing steps like storage, picking, and inventory management.
Types of Cross-Docking Facilities
1. Traditional I-Shaped Facilities
- Long, narrow buildings with docks on opposite sides
- Typical size: 50,000-200,000 sq ft
- Best for: Direct transfer operations with minimal sorting
2. L-Shaped Facilities
- Docks arranged in an L-configuration
- Typical size: 30,000-100,000 sq ft
- Best for: Operations that require some staging and organization
3. U-Shaped Facilities
- Three-sided dock arrangement
- Typical size: 75,000-250,000 sq ft
- Best for: Complex sorting operations with multiple product categories
4. T-Shaped Facilities
- Central receiving area that branches to multiple shipping wings
- Typical size: 100,000-300,000 sq ft
- Best for: Hub-and-spoke distribution networks
When Cross-Docking Makes Sense for Your Business
Cross-docking isn’t right for every operation. Here’s when it makes the most business sense:
Ideal Product Types:
- High-volume, consistent products
- Perishable goods needing a quick turnaround
- Pre-packaged, ready-to-ship items
- Staple products with predictable demand
- Products already sorted or palletized by destination
Best Business Scenarios:
- Retail distribution networks with many store locations
- Just-in-time manufacturing operations
- Perishable goods distribution (food, flowers, etc.)
- Parcel carriers consolidating deliveries
- E-commerce businesses with predictable shipping patterns
When Traditional Warehousing May Be Better:
- Low or unpredictable order volumes
- Products requiring inspection, repackaging, or value-added services
- Items with long shelf lives and steady demand
- Specialized storage requirements (temperature control, security, etc.)
- Businesses without reliable supply chain visibility
Business Benefits of Cross-Docking
1. Cost Reduction
- 25-30% lower handling costs compared to traditional warehousing
- Reduced inventory holding costs (potentially 20-30% savings)
- Lower space requirements (and associated real estate costs)
- Decreased labor costs for picking and storage operations
2. Speed and Efficiency
- Typical transit time reduction: 2-3 days
- Reduced touch points (3-5 fewer handling steps)
- Faster order-to-delivery cycles
- Reduced opportunity for handling damage
3. Inventory Management
- Less inventory on hand (reduced by 35-45% in many cases)
- Lower risk of obsolescence for seasonal or trendy items
- Reduced inventory shrinkage
- Better alignment with just-in-time strategies
4. Customer Satisfaction
- Fresher products with longer shelf life at the destination
- More consistent availability of products
- Faster delivery times
- Potential for more frequent deliveries
Key Facility Requirements for Effective Cross-Docking
1. Physical Characteristics
- Sufficient dock doors: Typically 1 door per 2,500-3,000 sq ft
- Column spacing: 50’+ preferred for maneuvering space
- Clear height: 28-32′ minimum
- Floor quality: Heavy-duty concrete (6″+) with minimal cracks
- Yard space: Extensive trailer parking and maneuvering area
2. Layout Considerations
- Dock height: Standard 48-52″ dock height
- Dock levelers: Hydraulic levelers for various truck heights
- Staging areas: Space for temporary product organization
- Flow design: Minimal cross-traffic between inbound and outbound
3. Technology Infrastructure
- Robust power: Support for conveyor systems and equipment
- Network connectivity: High-speed data for scanning and tracking
- Lighting: Proper illumination for accurate sorting
- Climate considerations: Appropriate for product requirements
Finding the Right Cross-Docking Facility
Location Factors to Prioritize
1. Transportation Network Access
- Proximity to major highways: Ideally within 1-2 miles
- Minimal traffic congestion: Analyze rush hour patterns
- Alternative route options: Backup routes for emergencies
- Distance from supplier/destination hubs: Central to your network
2. Labor Availability
- Workforce with logistics experience
- Population density within commuting distance
- Competitive wage rates for warehouse workers
- Availability of logistics management talent
3. Regional Considerations
- Weather patterns: Avoid areas prone to regular disruptions
- Local regulations: Check for restrictions on hours of operation
- Future development plans: Research area growth projections
- Tax incentives: Some regions offer logistics advantages
Evaluating Potential Properties
Create a scoring matrix for potential facilities with these categories:
- Location suitability (0-25 points)
- Proximity to transportation network
- Centrality to your distribution area
- Local infrastructure quality
- Physical characteristics (0-25 points)
- Number and layout of dock doors
- Building dimensions and clear height
- Yard space and trailer parking
- Cost factors (0-20 points)
- Lease or purchase price
- Operating costs (utilities, taxes, etc.)
- Improvement requirements and costs
- Operational efficiency (0-20 points)
- Internal flow potential
- Loading/unloading efficiency
- Staging space adequacy
- Future flexibility (0-10 points)
- Expansion potential
- Lease terms and options
- Adaptability to changing needs
Setting Up Your Cross-Docking Operation
Essential Equipment
- Conveyor systems: Basic to sophisticated sorting conveyors
- Barcode scanners and RFID technology: For tracking and sorting
- Dock equipment: Levelers, shelters, bumpers, and trailer restraints
- Material handling equipment: Forklifts, pallet jacks, and carts
- Software systems: Warehouse management and yard management solutions
Staffing Requirements
Typical positions needed for a mid-sized cross-docking operation:
- Dock supervisors: 1-2 per shift
- Material handlers: 10-20 depending on volume
- Forklift operators: 5-8 per shift
- Administrative staff: 2-3 for documentation and coordination
- Management team: 3-5 for overall facility operation
Implementation Timeline
A typical cross-docking setup follows this timeline:
- Months 1-2: Facility selection and lease negotiation
- Months 2-3: Basic infrastructure setup and equipment installation
- Month 4: Software implementation and integration
- Month 5: Staff hiring and training
- Month 6: Pilot operations with limited volume
- Months 7-8: Scaling to full operational capacity
Cross-Docking Success Strategies
1. Start with Clear Metrics
Establish KPIs for:
- Dock-to-dock time (target: under 24 hours)
- Cost per handled unit
- Error rates and accuracy
- Labor productivity
2. Implement the Right Technology
- Barcode or RFID tracking systems for real-time visibility
- Automated sortation for high-volume operations
- Yard management software to coordinate truck movements
3. Develop Strong Supplier Relationships
- Establish clear receiving schedules
- Create standardized labeling and palletization requirements
- Develop communication protocols for exceptions
4. Design for Flexibility
- Create modular sorting areas that can be reconfigured
- Plan for peak season volume increases (typically +40-60%)
- Consider future expansion needs in the initial layout
Common Challenges and Solutions
Challenge: Handling Exceptions
Solution: Designate a specific area for non-standard items and a team to handle exceptions without disrupting the main flow.
Challenge: Peak Volume Management
Solution: Create flexible staffing models and temporary staging areas that can be activated during high-volume periods.
Challenge: Coordination Between Partners
Solution: Implement shared visibility systems that allow suppliers and recipients to track shipments and anticipate arrivals.
Challenge: Quality Control
Solution: Establish sampling-based inspection protocols that don’t slow down the cross-docking process while maintaining quality standards.
Real-World Applications of Cross-Docking
Retail Distribution
Major retailers use cross-docking to consolidate shipments from multiple vendors into store-specific deliveries, reducing inventory holding costs by 25-30% while improving stock availability.
Food Distribution
Fresh produce distributors utilize cross-docking to reduce transit time by up to 48 hours, extending shelf life and reducing spoilage by 15-20%.
Manufacturing Support
Auto manufacturers employ cross-docking for just-in-time delivery of components, reducing line-side inventory by up to 90% while ensuring production continuity.
E-commerce Fulfillment
Online retailers use cross-docking to consolidate orders from multiple fulfillment centers, reducing shipping costs by 15-25% while maintaining delivery speed commitments.
Conclusion: Is Cross-Docking Right for Your Business?
Cross-docking can dramatically improve logistics efficiency, but it’s not suitable for every operation. Consider these factors in your decision:
- Product characteristics: Stability, demand predictability, and handling requirements
- Supply chain visibility: Communication capabilities with suppliers and customers
- Volume consistency: Regular, predictable flows work best for cross-docking
- Network alignment: Geographic distribution of suppliers and customers
For businesses with the right conditions, cross-docking can offer significant competitive advantages through cost reduction, improved speed, and enhanced customer satisfaction.